Conveyor belt drives are essential in mining and mineral processing, facilitating the efficient transport of large volumes of materials. A mining conveyor belt plays a crucial role in maintaining operational efficiency, reducing downtime, and minimizing operational costs. These drives are designed to withstand harsh conditions and heavy loads, ensuring durability and reliability. Advanced technologies such as gearless drives and digital monitoring systems enhance performance and predictive maintenance. Case studies of Hutchinson Salt and Rohrer’s Quarry highlight the successful implementation of reliable conveyor systems, demonstrating their importance in maintaining continuous operation and enhancing productivity.
The Importance of Reliable Conveyor Belt Drives in Mining and Mineral Processing
overview:
- Essential Role in Industry:
- Conveyor belt drives are integral components in mining and mineral processing operations.
- They facilitate the efficient transport of large volumes of materials over varying distances.
- Critical for maintaining the flow of materials from extraction points to processing facilities.
- Operational Efficiency:
- Reliable conveyor belt drives ensure smooth and continuous operation.
- Minimize disruptions that can lead to costly downtimes and production losses.
- Directly impact the overall productivity and profitability of mining operations.
- Handling Harsh Conditions:
- Designed to withstand severe operating environments, including extreme temperatures, high humidity, and exposure to abrasive and corrosive materials.
- Robust construction to handle heavy loads and high impact from falling rocks and other materials.
- Economic Benefits:
- Reduce operational costs by minimizing the need for frequent maintenance and replacements.
- Efficient material handling systems lower labor costs and increase throughput.
- Safety and Environmental Impact:
- Enhance safety by reducing the need for manual handling and truck haulage, thereby decreasing the risk of accidents.
- Environmentally friendly as they reduce the reliance on diesel-powered vehicles, lowering emissions and fuel consumption.
- Technological Advancements:
- Modern conveyor belt drives incorporate advanced technologies such as gearless drives and digital monitoring systems.
- Improve performance through predictive maintenance, real-time monitoring, and data analytics.
Key Benefits of Reliable Conveyor Belt Drives:
- High Reliability:
- Essential for maintaining continuous operations in mining and mineral processing.
- Prevent unexpected breakdowns that can halt production and incur significant financial losses.
- Durability:
- Built to last in the most demanding conditions.
- Use of high-quality materials and advanced manufacturing techniques to enhance longevity.
- Efficiency:
- Optimized for energy efficiency, reducing operational costs and environmental impact.
- High-performance drives ensure that material transport is efficient and consistent.
- Maintenance:
- Designed for ease of maintenance, with features that facilitate quick and easy repairs.
- Advanced splicing techniques and strong bonding ensure minimal maintenance requirements and extended service life.
- Customization:
- Tailored solutions to meet the specific needs of different mining operations.
- Options for different belt widths, lengths, materials, and configurations to optimize performance for particular applications.
Applications in Mining and Mineral Processing:
- Surface Mining:
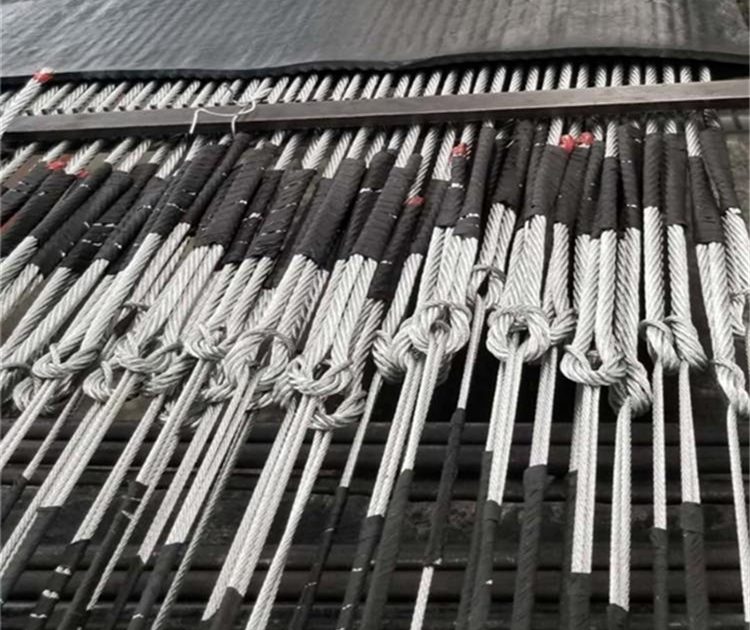
- Used to transport overburden and extracted minerals from the mining face to processing facilities, a steel cold conveyor belt is essential for large-scale mining operations where material needs to be moved over long distances.
- This type of conveyor belt provides the necessary strength and durability to handle heavy loads and harsh conditions typically found in mining environments.
- Underground Mining:
- Provide a reliable means of transporting materials to the surface.
- Designed to navigate the confined spaces and complex layouts of underground mines.
- Material Processing:
- Integral in the various stages of mineral processing, including crushing, grinding, and separation.
- Ensure a steady flow of materials through processing plants, improving efficiency and output.
Case Studies:
Hutchinson Salt Case Study
Location and Background:
- Location: Hutchinson, Kansas, USA.
- Background:
- Hutchinson Salt operates an underground mine and loading facility that has been active since 1923.
- The company is involved in the mining, storage, and shipping of millions of tons of salt throughout the Midwest.
- Hutchinson Salt’s operations are critical for supplying salt for road deicing, water conditioning, agricultural feed, and various industrial applications.
- The facility’s continuous operation is crucial to meet the demand, requiring highly reliable and durable equipment.
Challenge of Operating in Corrosive Environments:
- Corrosive Properties of Salt:
- Salt’s corrosive nature poses significant challenges to conventional conveyor systems.
- Continuous exposure to salt can lead to rapid deterioration of mechanical components, causing frequent breakdowns and increasing maintenance costs.
- Operational Continuity:
- Any downtime in conveyor operation would disrupt the loading of trains and trucks, leading to significant operational inefficiencies and potential delays in supply.
- Environmental Harshness:
- The harsh mining environment, characterized by high dust levels and abrasive materials, adds to the difficulty in maintaining reliable conveyor systems.
Solution: Implementation of Internally-Powered, Hermetically-Sealed Motorized Pulleys:
- Advantages of the Solution:
- Corrosion Resistance: The hermetically-sealed design protects internal components from the corrosive effects of salt, significantly extending the lifespan of the pulleys.
- Reduced Maintenance: The sealed construction minimizes the ingress of contaminants, reducing wear and tear on internal components, leading to lower maintenance requirements and less downtime.
- Enhanced Reliability: The internally-powered design eliminates the need for external motors and gearboxes, which are prone to failure in corrosive environments, resulting in a more reliable and efficient conveyor system.
- Energy Efficiency: Motorized Pulleys are designed to be energy-efficient, reducing overall energy consumption and operational costs.
Rohrer’s Quarry Case Study
Location and Background:
- Location: Eastern Pennsylvania, USA.
- Background:
- Rohrer’s Quarry has been involved in the extraction, crushing, and shipping of rock for over 50 years.
- The quarry supplies materials for the construction of roads, bridges, and buildings in the Eastern United States.
- The quarry’s operation is vital for local infrastructure projects, necessitating efficient and reliable material handling systems to meet production demands.
Challenge of Efficient Drive for a 1,000-Foot-Long Belt Conveyor:
- Operational Requirements:
- The quarry required a reliable and efficient drive system for a 1,000-foot-long belt conveyor in the pit.
- The drive system needed to enhance operational efficiency by ensuring smooth and continuous transport of crushed rock from the extraction site to processing areas.
- Mechanical Strain:
- The length and heavy load of the conveyor placed immense strain on the drive system, necessitating a solution that could handle high tension and heavy-duty operations.
Solution: Dual 150 HP Motorized Pulleys Reducing Belt Tension and Cost:
- Motorized Pulleys:
- Rulmeca was consulted based on their previous successful implementations of Motorized Pulleys.
- Despite an initial request for a single 300 HP drive, Rulmeca recommended a solution involving two 150 HP Motorized Pulleys with a belt speed of 600 feet per minute.
- Advantages of the Dual Drive System:
- Reduced Belt Tension: By using two 150 HP Motorized Pulleys, the load was more evenly distributed across the conveyor belt, significantly reducing the overall belt tension.
- Cost Efficiency: The dual-drive setup decreased the initial cost of the belt and extended its service life by reducing mechanical stress and wear.
- Enhanced Reliability: The Motorized Pulleys provided consistent and reliable power, ensuring smooth operation and minimizing the risk of breakdowns.
- Improved Performance: The system’s design allowed for higher operational efficiency, ensuring that the quarry could meet its production targets without interruptions.
- Implementation and Results:
- The implementation of the dual 150 HP Motorized Pulleys resulted in high satisfaction from Rohrer’s Quarry.
- The system provided a reliable and cost-effective solution, enhancing the quarry’s operational efficiency and ensuring the continuous transport of materials.
Key Takeaways:
Specialization in Internally-Powered Motorized Pulleys
1. Advanced Design and Engineering:
- Innovative Technology:
- Internally-powered Motorized Pulleys are a cutting-edge solution that integrates the motor and drive components within the pulley shell itself. This design minimizes the number of external moving parts, reducing the risk of mechanical failure.
- Compact and Efficient:
- The compact design of Motorized Pulleys eliminates the need for external motors, gearboxes, and couplings, resulting in a more streamlined and efficient conveyor system. This design saves space and reduces the complexity of the installation.
- Enhanced Durability:
- By housing the motor inside the pulley, Motorized Pulleys are protected from environmental contaminants such as dust, water, and corrosive materials. This protection significantly extends the lifespan of the drive system.
2. Performance and Reliability:
- Consistent Power Delivery:
- Motorized Pulleys deliver consistent and reliable power to the conveyor belt, ensuring smooth operation and minimizing downtime. This reliability is crucial for maintaining continuous production in industrial environments.
- Energy Efficiency:
- The integrated design of Motorized Pulleys reduces energy loss associated with traditional drive systems, making them more energy-efficient. This efficiency leads to lower operational costs and a smaller environmental footprint.
- Low Maintenance:
- With fewer exposed components, Motorized Pulleys require less maintenance compared to conventional conveyor drive systems. This reduction in maintenance needs translates to lower labor costs and increased uptime.
Tailored Solutions for Harsh, Corrosive, and Abrasive Conditions
1. Customization to Meet Specific Needs:
- Material Selection:
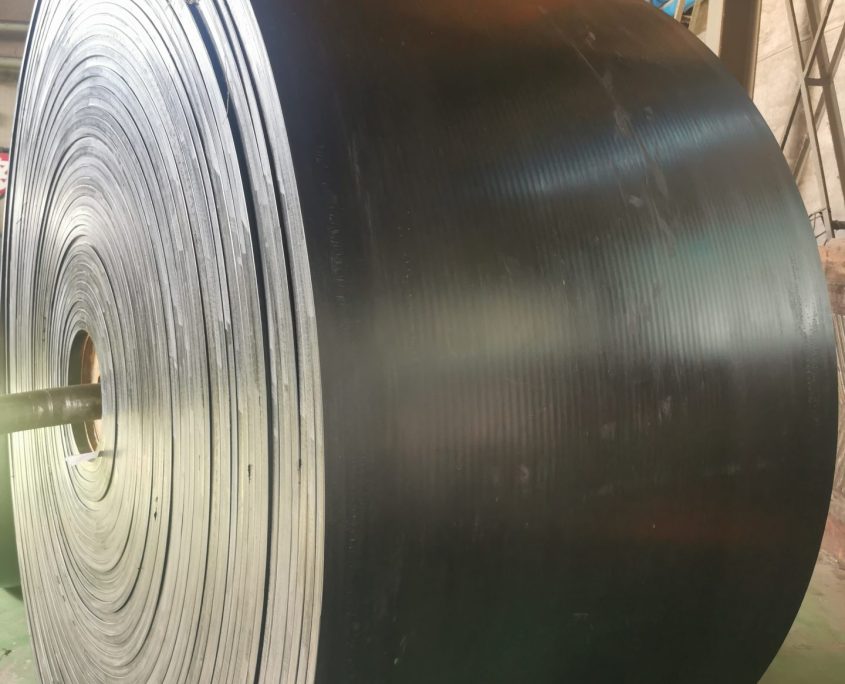
- Motorized Pulleys can be customized with materials that are resistant to specific environmental challenges. For example, stainless steel or specially coated pulleys can be used in corrosive environments to prevent rust and degradation. Additionally, pairing these pulleys with specialized conveyor belts, such as a steel cord conveyor belt or a nylon conveyor belt, can further enhance their performance and durability in demanding conditions.
- Seal and Protection Systems:
- Advanced sealing technologies are employed to protect the internal components from harsh conditions. Hermetically-sealed designs prevent the ingress of dust, water, and chemicals, ensuring the integrity of the motor and drive components.
- Temperature Resistance:
- For operations involving extreme temperatures, Motorized Pulleys can be designed with materials and cooling systems that withstand high heat or cold conditions without compromising performance.
2. Application-Specific Designs:
- Mining and Quarrying:
- In mining and quarrying applications, Motorized Pulleys are built to handle heavy loads and resist the abrasive effects of materials like ore and crushed stone. The robust construction ensures longevity and reduces the frequency of replacements.
- Food Processing:
- For food processing, where hygiene is paramount, Motorized Pulleys are designed with smooth surfaces and materials that resist contamination and are easy to clean. These pulleys meet stringent food safety standards.
- Chemical Processing:
- In chemical processing plants, Motorized Pulleys are equipped with corrosion-resistant materials and coatings to withstand exposure to aggressive chemicals. This customization ensures reliable operation and safety in hazardous environments.
Problem-Solving Capabilities and Customer Partnerships for Reliable and Long-Lasting Equipment
1. Collaborative Approach:
- Customer Engagement:
- Rulmeca and similar companies prioritize working closely with customers to understand their unique challenges and operational requirements. This engagement involves site visits, consultations, and detailed assessments to tailor solutions effectively.
- Bespoke Solutions:
- By collaborating with customers, these companies can design and implement bespoke Motorized Pulley solutions that address specific issues such as space constraints, environmental hazards, and operational demands.
2. Engineering Expertise:
- Technical Support:
- Providing comprehensive technical support is a key aspect of customer partnerships. This support includes installation guidance, maintenance training, and troubleshooting assistance to ensure the smooth operation of Motorized Pulleys.
- Continuous Improvement:
- Engineering teams continuously seek feedback from customers to improve product designs and performance. This iterative process ensures that Motorized Pulleys remain at the forefront of technology and meet evolving industry needs.
3. Long-Term Reliability and Cost-Effectiveness:
- Durable Construction:
- The use of high-quality materials and advanced manufacturing techniques ensures that Motorized Pulleys are durable and capable of withstanding harsh operating conditions over long periods.
- Reduced Total Cost of Ownership:
- The long lifespan and low maintenance requirements of Motorized Pulleys contribute to a reduced total cost of ownership. Customers benefit from lower operational expenses and fewer disruptions due to equipment failure.
4. Case Study Examples:
- Hutchinson Salt:
- In the Hutchinson Salt case study, the implementation of internally-powered, hermetically-sealed Motorized Pulleys provided a reliable solution for a highly corrosive environment. This customization ensured continuous operation and reduced maintenance needs.
- Rohrer’s Quarry:
- At Rohrer’s Quarry, the use of dual 150 HP Motorized Pulleys addressed the challenge of efficiently driving a 1,000-foot-long conveyor belt. The solution reduced belt tension and initial costs, showcasing the problem-solving capabilities and customer-centric approach of the provider.
5. Industry Recognition:
- Proven Track Record:
- The successful implementation of Motorized Pulleys in various industries, from mining to food processing, demonstrates their versatility and effectiveness. Case studies and customer testimonials highlight the reliability and performance of these solutions.
- Compliance with Standards:
- Motorized Pulleys often meet or exceed industry standards and certifications, providing customers with confidence in their quality and suitability for demanding applications.